Introduction
Distillation columns are the backbone of separation processes in specialty chemicals, pharmaceuticals, and other industrial environments. They enable the precise separation of complex mixtures into high-purity products, which is essential for product quality and regulatory compliance.
Discussions with industry leaders have uncovered the persistent challenges that operators face: maintaining product purity, minimizing energy consumption, and maximizing throughput, all while responding to fluctuating feedstocks and market demands.1
Artificial intelligence (AI) is emerging as a transformative solution for enhancing the performance of distillation columns. By leveraging hybrid modeling for distillation simulation, soft sensing for quality measurement, and real-time process optimization, AI can address these challenges head-on.
In this article, we’ll explore how Basetwo’s AI-enabled technology enables real-time quality prediction and process optimization to drive measurable improvements in distillation column efficiency.
Importance of Distillation Column Efficiency
Distillation column efficiency refers to the ability of a column to achieve the desired separation with minimal energy input and maximum throughput.2 High efficiency means more product is recovered at the required purity faster, with less waste and lower operational costs.
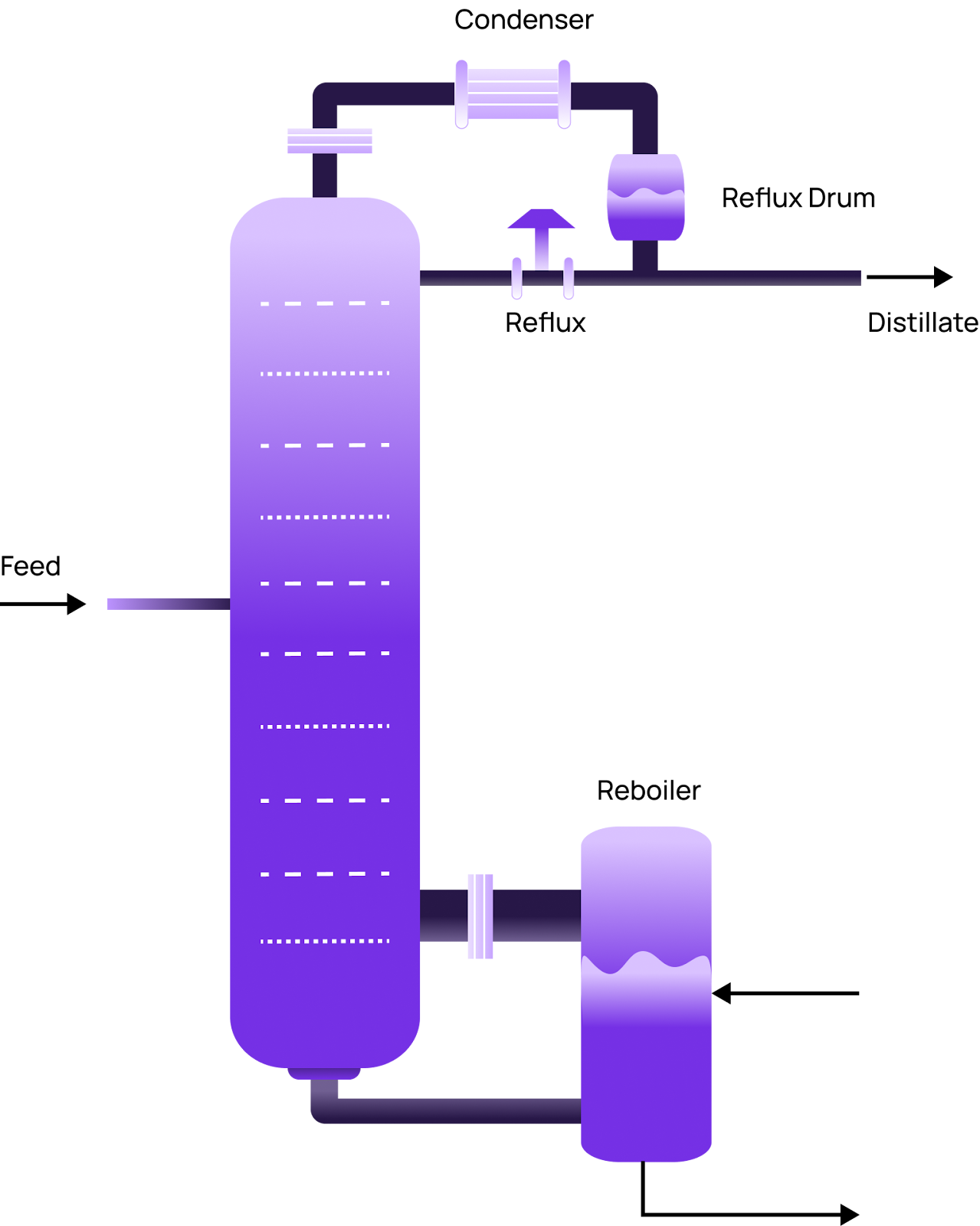
Suboptimal operation can have significant financial and operational consequences. Inefficient columns consume excess energy, drive up utility costs, and may produce off-spec products that require costly reprocessing or disposal.3 In industries where margins are tight and regulatory compliance is crucial, improving distillation column efficiency has a clear business benefit.
Soft Sensing of Quality Attributes in a Distillation Column
Soft sensing uses historical process data (e.g., temperature, pressure, flow rates) fed into AI-enabled models to infer hard-to-measure variables, such as product purity, viscosity, or composition.4
Instead of waiting for lab results, operators can access real-time identification and prediction of key quality attributes, enabling faster and more informed process adjustments.
AI-Enabled Digital Twins for Distillation Column Optimization
In this scenario, an AI-enabled digital twin would act as a virtual replica of the distillation column process. Digital twins allow specialty chemicals companies to virtually test various operational scenarios, such as changes in flow rates, temperature, etc.5
This reduces the need for costly and time-consuming physical experiments on large-scale columns, expediting process optimization and enabling rapid identification of optimal operating conditions.
To ensure the model accurately reflects the company’s process, engineers can develop a hybrid model that combines physics-based principles with data-driven insights, effectively capturing both measurable variables and complex process dynamics.6
Predicting Product Quality in Real-Time with Soft Sensing: A Specialty Chemical Use Case
To explore soft sensing for quality attributes, we can look at one of Basetwo’s customers who leveraged their AI-enabled digital twin platform in their specialty chemical processes.
AI-powered soft sensors can predict product purity continuously, eliminating the delays and costs associated with traditional lab testing. In this scenario, soft sensing enabled this global specialty chemical manufacturer to measure purity, a variable that was previously only measured at the end of each cycle, throughout the duration of their entire batch.
By enabling real-time insights into their key quality attributes, they were able to determine when the batch had reached its optimal purity target. As a result, the company avoided batch overruns and reduced its cycle times by 30%.
From there, they leveraged the hybrid model of their distillation process to identify any process deviations and ensure their batch was running smoothly at all times. The model was able to detect deviations in variables, like temperature, and identify the effect on quality variables like purity.
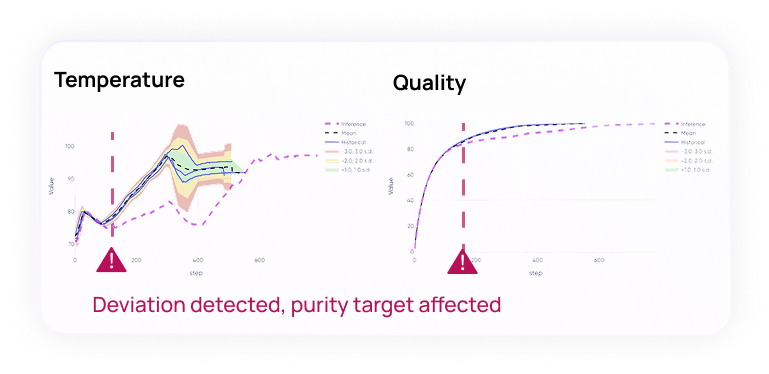
In this way, the company was able to implement corrective actions, which resulted in an 80% reduction in batch failures and an annual savings of 750k for a single product.7
Explore the use case here.
Getting Started with AI in Distillation Operations
Data requirements:
- Reliable, high-frequency data from temperature, pressure, flow, and composition sensors.
- Lab data: Historical quality measurements for model training and validation.
- Performance history: Operational data to identify patterns and optimize control strategies.
Piloting a first project
Begin with a pilot project on a single column or production line. This approach allows teams to validate AI models, demonstrate value, and build confidence before scaling up. Digital twin platforms, like Basetwo, have distillation column model templates built into the software, enabling engineers to achieve accurate process modeling in weeks.
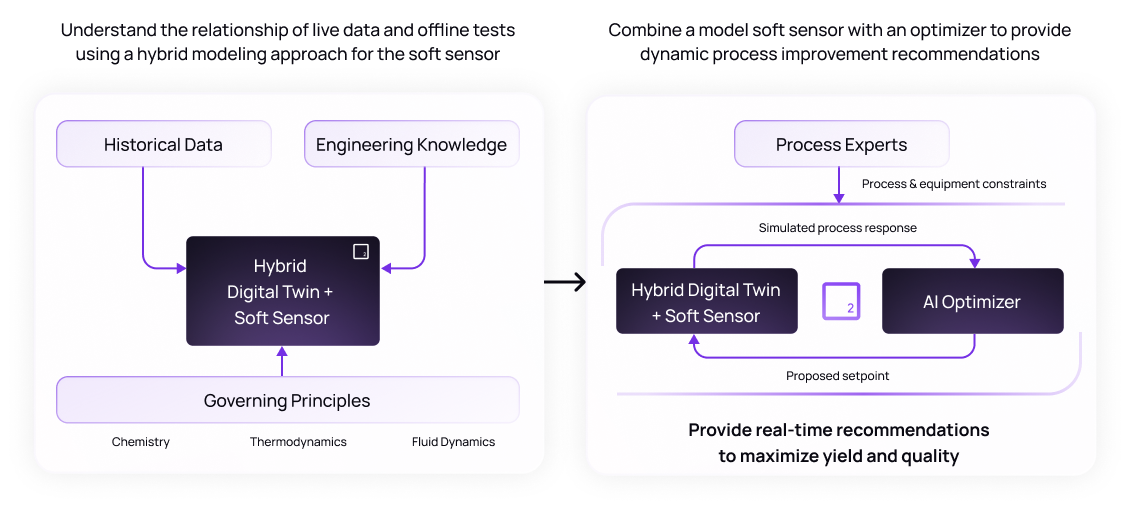
Conclusion
AI is revolutionizing distillation column efficiency by enabling real-time quality prediction and process optimization. The results are clear: maintained product quality, lower energy consumption, increased throughput, and substantial cost savings.
As industries face increasing pressure to improve both profitability while staying competitive, AI offers a practical path forward.
To explore AI in your specialty chemicals processes, book a time with Basetwo today.
FAQs
1. How to Improve Distillation Column Efficiency with AI?
Improving distillation column efficiency with AI involves a layered approach: Soft sensing for quality prediction: Use AI models to infer product quality in real time, enabling faster and more accurate process adjustments. Real-time optimization for sustainable performance: Implement AI-driven optimization engines that continuously adjust operating parameters for maximum efficiency and product quality. AI provides unprecedented visibility, adaptability, and continuous improvement—empowering operators to achieve new levels of performance and sustainability.
References:
- BM Engineering. (n.d.). How to improve distillation column efficiency through process control. Retrieved June 24, 2025, from https://www.bmengineering.co.uk/how-to-improve-distillation-column-efficiency-through-process-control/
- Green, D. W., & Southard, M. Z. (Eds.). (2019). Perry's Chemical Engineers' Handbook (9th ed., Section 13: Distillation). McGraw-Hill Education.
- Kister, H. Z. (1992). Distillation Design. McGraw-Hill.
- Silva, C., Silva, J. L. P., & Mendes, R. (2022). Deep Reinforcement Learning for Chemical Process Control: Distillation Column Case Study. arXiv. https://arxiv.org/ftp/arxiv/papers/2208/2208.04373.pdf
- Vadiee, A., & Soroush, M. (2024). Integrating AI with process control. Chemical Engineering Progress, 120(1). Retrieved from https://www.aiche-cep.com/cepmagazine/january_2024/MobilePagedArticle.action?articleId=1941203#articleId1941203
- Wang, J., & Gu, Q. (2024). A hybrid data-model-driven approach for fault diagnosis in distillation columns. Computers & Chemical Engineering, 186, 108828. https://doi.org/10.1016/j.compchemeng.2024.108828
- Basetwo AI. (2025). Homepage. Retrieved June 24, 2025, from https://www.basetwo.ai